When operations experience occasional jamming in their case formers, they are often quick to blame these problems on the machine. However, we often see that inconsistencies with corrugated flats are the true culprit.
While case formers have impressive capabilities to radically increase box quality and output, operators need to remember that they are just machines. A warped case that’s obvious to a human eye and can be removed by an employee may not be noticed by the machine, which can lead to a potential jam. Proper management before the cases are fed into the machine can be critical to reducing costly stoppages, and it starts with understanding these two factors:
1: Paper Type
Corrugate cases, in the simplest terms, are built from several layers of paper glued together. This paper can either be new, otherwise known as “virgin” material, or recycled. As paper is used and recycled multiple times, it becomes more likely to see warping and inconsistencies, leaving your machine vulnerable to jams. This is especially true when the products packaged in the case are heavier and place more strain on the corrugate.
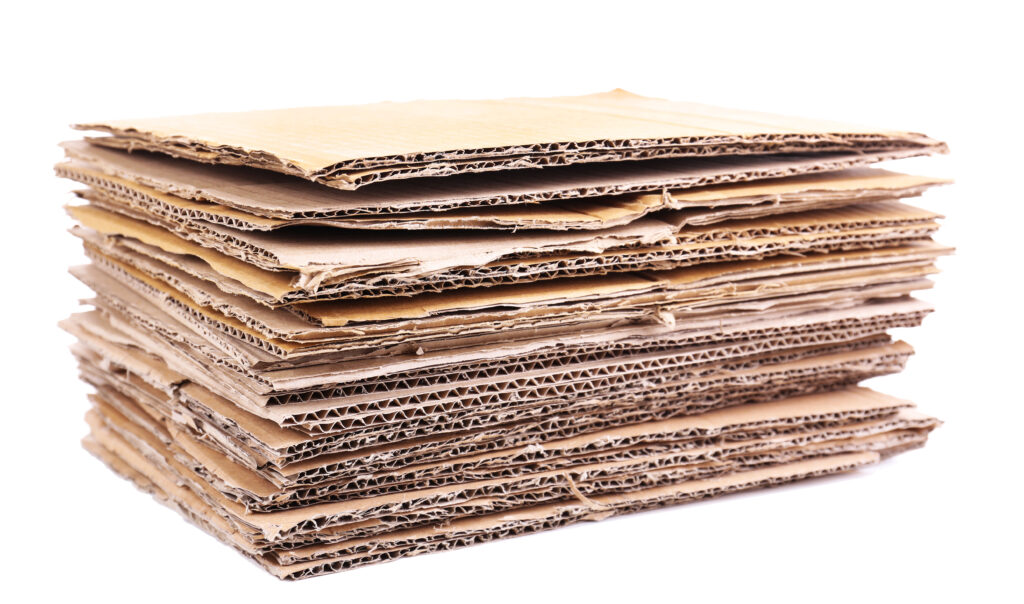
Paper has its limits on how many times it can be recycled and still be usable, but that doesn’t mean that recycled boxes should not be used. It simply means that companies utilizing recycled boxes need to be more conscious of potential inconsistencies and more deliberate in their efforts to avoid them.
2: Storage
Corrugate quality is additionally impacted by how bundles of flats are transported and stored. Being intentional in this area is particularly important with recycled cases, but all kinds of paper benefit from proper management before they are fed into the machine. Before case flats are shipped to an end-user customer, they are typically bundled or stacked together with straps. Putting a lot of tension on those bundling straps can help condense the cases for shipping, but it can also place excessive strain on the corrugate that is often released through warping. This can be compounded by humidity. If flats are stored in a humid environment, they will soak up that water in the air, which leaves boxes susceptible to wavy dents in the material caused by either the straps or other boxes stacked on top pushing out that moisture. Lastly, pallets of cases are also often stretch wrapped during transportation to protect the load. However, if the tension is too high on the stretch wrap, it can also cause cases to be warped especially in corners of the pallet.
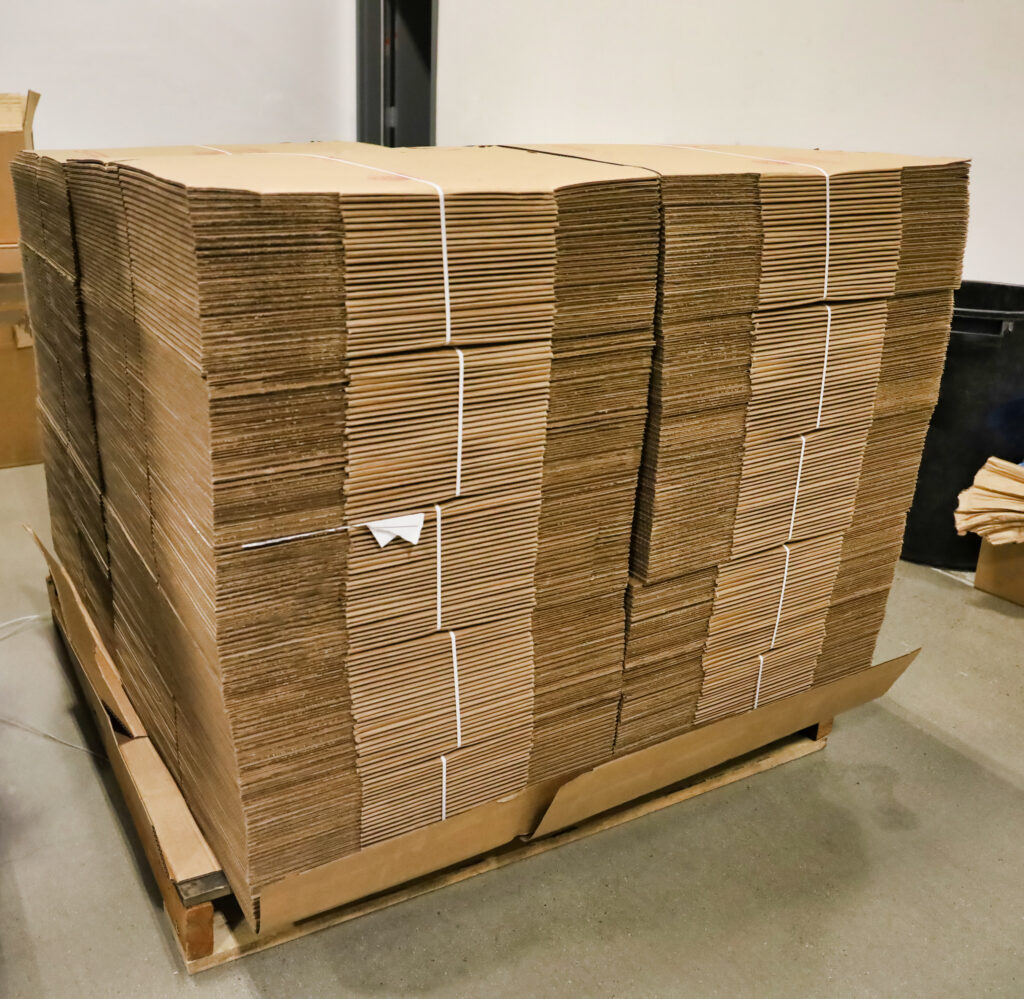
Working with your corrugator or box provider that wraps flats loosely and storing unformed boxes in a dryer area are two easy ways to boost consistency and reduce jams.
Compensating Through Better Machinery
As recycled corrugated is not only better for the environment but better for costs, you can also opt for case forming machinery that utilizes technologies that are able to handle more variance in corrugated. An example of this is Wexxar Bel’s patented Pin & Dome technology. Their unique case handling method involves the machine inserting metal pins into the flutes of the case, mechanically grabbing and opening the case, providing a superior method of case opening than traditional vacuum cup technology. The pins also do not wear over time, unlike vacuum cups which can harden over use and is also highly susceptible to elements surrounding the machine such as dust and temperature.
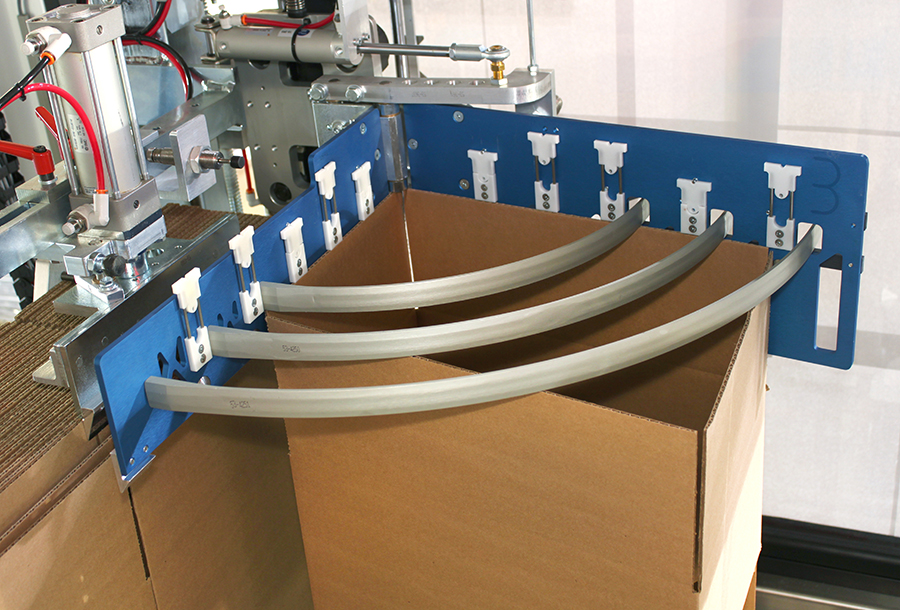
Combining more forgiving machines with proper case management is the best “case” scenario for effective, efficient case forming. Talk to a Wexxar Bel representative to put all these strategies to work in your operation.
Bill Sebok is a Midwest Regional Sales Manager for Wexxar Bel (www.wexxar.com). He can be reached at Bill.sebok@promachbuilt.com.